Clockwork Echoes: The Lost Art of Toymaker's Precision
There's a peculiar magic that clings to antique cast iron toys. Not just the inherent charm of a bygone era, but a tangible sense of skilled hands, unwavering patience, and a level of craftsmanship seemingly lost to the relentless march of mass production. Holding a meticulously detailed horse-drawn carriage, a sturdy fire engine, or a playful clown, you’re not simply admiring a toy; you’re touching a fragment of history, a testament to the dedication of the artisans who poured their talent into these enduring creations.
My grandfather, a quiet man of few words, possessed a small collection of these toys. I remember, as a child, spending hours mesmerized by them, carefully tracing the lines of the horses' harnesses and the intricate details of the firemen’s helmets. They weren’t just playthings; they were stories waiting to be unfolded, glimpses into a world of imagination and ingenuity. It was through him, I believe, that I developed a deep appreciation for the artistry and engineering that went into creating these miniature wonders.
The story of cast iron toys begins in the mid-19th century, a period of rapid industrialization and burgeoning middle-class leisure time. Before this, toys were largely handmade, often crafted from wood or pottery – beautiful, certainly, but fragile and relatively expensive. The advent of cast iron offered a revolutionary combination of durability, affordability, and the ability to reproduce intricate designs on a scale never before seen.
The Rise of the Toymakers
Early pioneers like Ives, J.K. Finch, and Whitlock & Sears spearheaded the cast iron toy industry in America. In Europe, firms like Armand & F. Co. in France, and Bing in Germany, dominated the market. These weren't simply factories; they were workshops filled with skilled patternmakers, molders, and finishers. Patternmakers, the unsung heroes of the process, painstakingly carved wooden models – the original blueprints for each toy. These patterns were then used to create molds, typically made of sand packed tightly around a core. The molten iron, poured into the molds, cooled and solidified, yielding a rough casting.
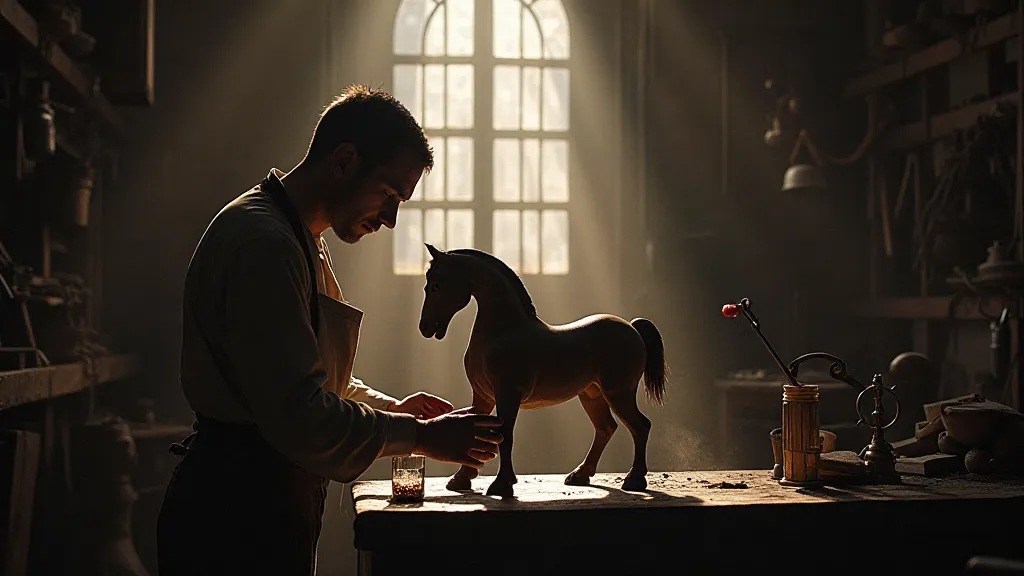
What truly set these toy makers apart was the level of detail they achieved. The process involved significant handwork. After the casting emerged from the mold, it was painstakingly cleaned and deburred. Then came the finishing – a series of meticulous steps that included filing, sanding, and painting. Many toys received multiple layers of paint, often with delicate hand-applied details like facial expressions or decorative scrollwork. The quality of the paint itself was also remarkable – often vibrant and resistant to chipping, a testament to the pigments used and the care taken in their application. This wasn't a matter of churning out hundreds of identical items; it was about crafting individual pieces with character and charm.
The Intricate Craft of Finishing
Consider a typical cast iron fire engine. It’s not merely a block of iron shaped like a truck. It's a miniature work of art, complete with rotating wheels, a working ladder, a bell that rings (often activated by a lever the child would operate), and a driver's seat with a tiny, but perfectly rendered, fireman. The complexity of such a toy demanded not just mechanical skill, but an eye for aesthetics. The design of the horses, the curvature of the carriages, the proportion of the figures – all these elements contributed to the toy's overall appeal.
The process of producing these toys was incredibly labor-intensive. Each toy passed through the hands of several skilled workers, each responsible for a specific task. It’s estimated that it took anywhere from 20 to 30 hours to produce a single, complex cast iron toy. This explains why, even at the height of their popularity, cast iron toys were considered a luxury item, accessible primarily to middle and upper-class families.
The decline of cast iron toy production began in the early 20th century. The rise of cheaper, mass-produced plastic toys, coupled with the disruptions caused by World War I and the Great Depression, gradually eroded the market for these handcrafted treasures. The skills needed to create them, once passed down through generations of artisans, began to fade.
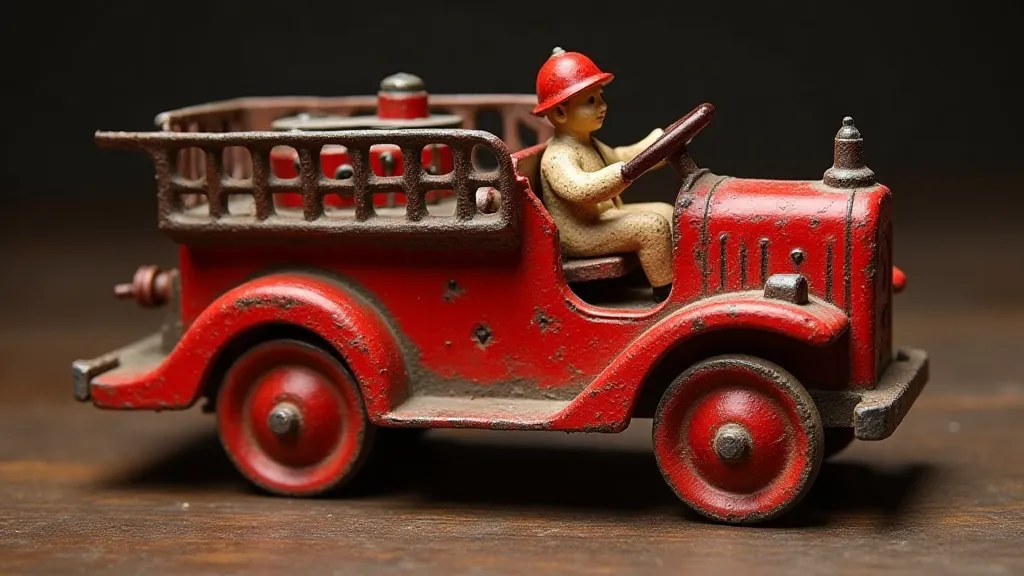
Preserving the Legacy
Today, antique cast iron toys are highly prized by collectors worldwide. Their rarity, combined with their undeniable beauty and historical significance, drives up their value. While pristine, untouched examples are incredibly rare and command top dollar, even toys with wear and tear can be captivating, bearing witness to the generations of children who once delighted in their playfulness.
For those drawn to collecting these miniature masterpieces, understanding the nuances of different manufacturers and their signature styles is key. Ives toys, for example, are known for their elaborate designs and intricate mechanisms, while J.K. Finch toys often feature charming animal figures. Researching the history of a particular toy, learning about its original cost, and examining its markings (often subtle, but crucial for identification) can significantly enhance the collecting experience.
The care and preservation of antique cast iron toys is also vital. While these toys are remarkably durable, they are still susceptible to rust and damage. Regular cleaning with a mild soap and water, followed by a light coating of wax, can help protect them from the elements. Storing them in a dry, climate-controlled environment is also essential. Occasionally, professional restoration may be necessary to repair broken parts or repaint faded areas, but it’s crucial to ensure that any restoration work is carried out by someone with expertise in this specialized field.
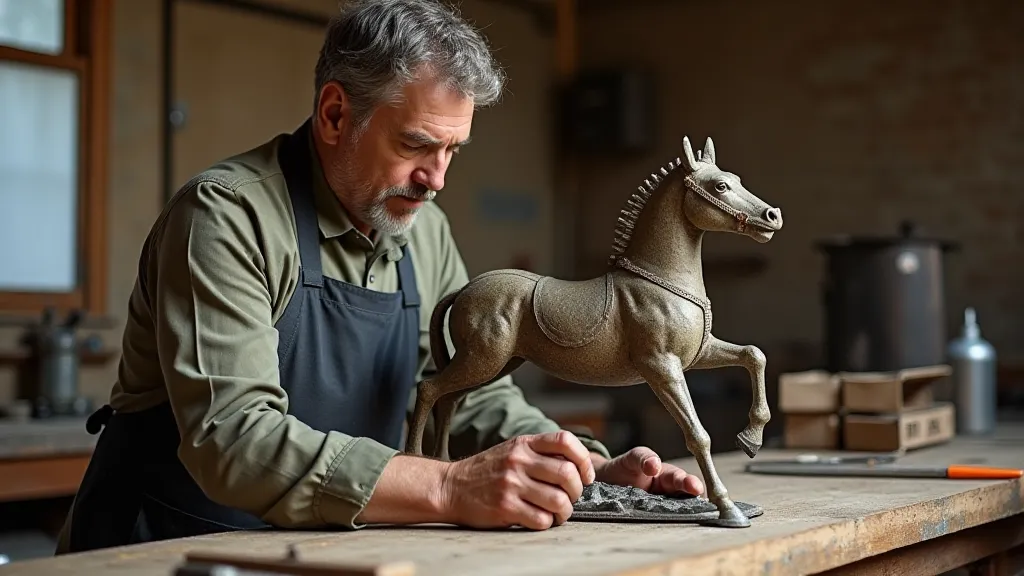
Ultimately, collecting antique cast iron toys is more than just acquiring objects of material value. It’s about connecting with a tangible piece of history, appreciating the artistry of a bygone era, and honoring the legacy of the skilled craftsmen who brought these miniature worlds to life. It’s about listening to the clockwork echoes of a lost art, and remembering a time when toys were cherished not just for their play value, but for the beauty and skill that went into their creation.